Corrosion Test Site Project Update
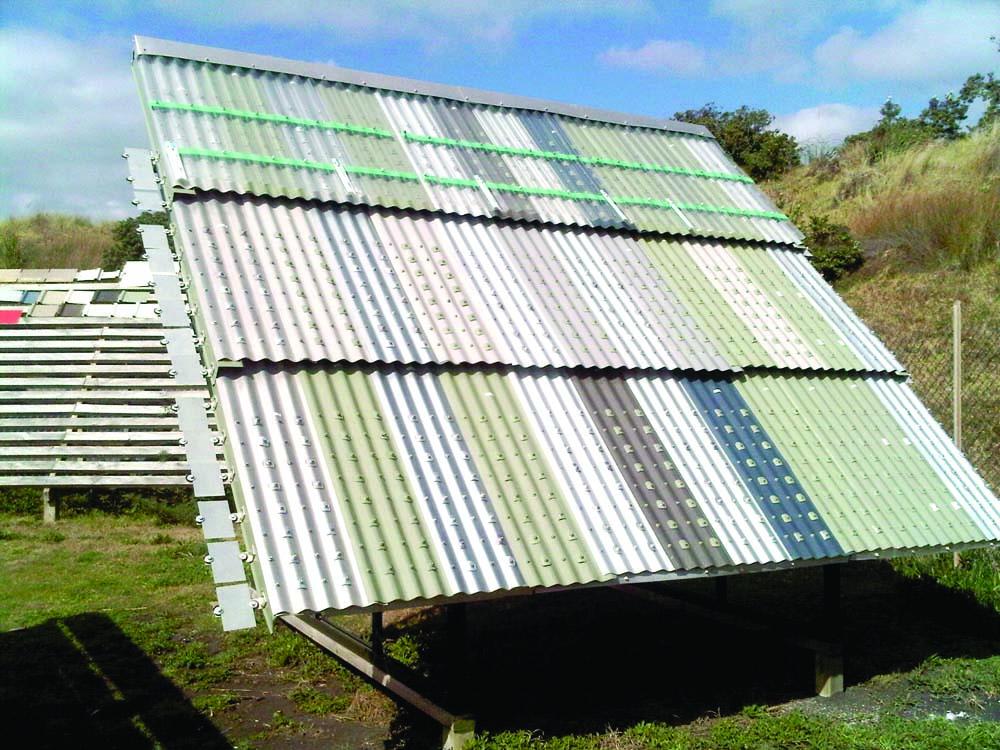
Once upon a time all metal roofs were made of 10-foot galvanised steel and fixed with lead-headed nails. Then we had longrun metal roofing while over the late 1980s and 1990s we have seen quite significant changes in both substrates and fasteners. This includes the introduction of COLORSTEEL® then Zincalume® and ZAM® type products and from lead-head to galvanised nails, and then screws.
By 2000 we were seeing issues with the fastener/substrate interface in marine environments. Early exposure trials indicated the need for better fasteners and better understanding of the reaction between substrate and fastener. NZMRM, with the substrate and fastener suppliers’ involvement, carried out the extensive trial reported on here. Having learned a lot from this we now have better products for new trials.
NZMRM’s Corrosion Project, which began in 2012, is the first initiative of its kind in New Zealand and the first to not be conducted by the manufacturers of any of the products and materials involved. The objective of the project is to determine the best combination of metal roofing systems (cladding, fasteners, underlay and flashing materials) for corrosion resistance and how the various components interact.
Given that roughly 80 per cent of housing in New Zealand is clad with roofs of longrun and its wide use on farm, industrial and commercial buildings, MRM’s considerable investment and on-going commitment to the project is directed to learning the causes of the deterioration that can occur when metal claddings are used in generally severe environmental conditions – mostly by the sea – and to determine how this can be avoided.
Valuable feedback
This research, started in 2012, has already provided valuable information for the industry by showing not only the best ways to carry out product exposure testing but to give guidance to the fastener and substrate manufacturers on what works and what doesn’t. And in the progress of this Corrosion Project, some additional and different objectives have emerged while developing the systems to be tested. These include fastener/substrate systems where neither corrodes; the effect of paint systems on metallic substrate and the effect of underlay and spacing/ventilation on the underside of corrosion.
More recently the project has benefitted from being able to involve new substrates and new, improved fasteners. Of most significance has been the emergence of new class five, coated steel fasteners for use in very severe environments – screws that should last 10 years or more in a Category 5 environment.
MRM’s considerable investment in the Corrosion Project, solutions from which are in tandem with on-going revision of the NZMRM Code of Practice, has recently been substantially reviewed. As with all research projects, over time the original concept for investigating corrosion of roofing materials has changed markedly. Some of the products assessed early on are no longer in use, or more importantly, have been superseded by improved versions that are considerably more robust – many as a result of early test results where the products did not fare so well.
In 2019 the trials are looking “potentially very good”; the testing is generating outcomes for corrosion that are better than in earlier trials. Factors need to be assessed or measured by using various standards and test methods, namely:
- Corrosivity of sites using several methods
- Quantifying the conditions under which a set of material exposure is subjected to over the period of the exposure
- Determining the effect of the exposure – visually and by other means
- Relating accelerated exposure at extreme sites to realistic conditions
A common problem in the roofing/fastener exposure projects is how to quantitatively assess corrosion of both components and the effects they have on each other. We developed a somewhat subjective method in 2017 on one test roof and this is being used for the remaining roofs as they are dismantled which we are progressively doing – the latest being Muriwai.
Test sites
The locations for the early trials were: Muriwai Golf Club (west coast) flat site 100m from the shore; Taharoa Ironsand Mine (west coast) elevated site 100m from breaking surf and adjacent to the NIWA weather station; Invercargill (south coast) gun club, sheltered site but close to the sea; Nelson (northern south island) Cawthron Institute, marine laboratory just behind Boulder Bank – exposed and severe; Waipu Golf Club (east coast) close to the sea next to a rusted shed. In addition, an aluminium roof site in New Plymouth was assessed up to 2015 but there were no test materials taken. Exposure sites are rated C1 – C5 – extended now to CX in accordance with ISO 9223.
The research team has ceased to monitor all except two West Coast sites; it having been demonstrated early on that east coast exposure, even when close to the sea, was far less severe than on the west coast. The exposure locations have been reviewed and while Taharoa remains as a location to assess corrosivity, a site at Limestone Downs farm is now the permanent exposure site. South of Port Waikato, Limestone Downs is owned by the Alma Baker Charitable Trust and the site is difficult to access with visits only possible between November and April each year. This extremely exposed and often inaccessible site at Limestone Downs has been assessed by using mild steel plates as CX screw of ISO 9223 (the most severe category and which is double the severity C5). This will enable the assessment of the NZMRM-suggested Class 5 screw much more quickly.
To ensure its suitability mild steel coupons were placed at Limestone Downs and also in parallel at New Zealand Steel’s Waikato North Head mine site and both sets of LD and NH coupons have now been replaced and will continue to be on-going, aligning with exposure of various materials.
How was the testing carried out?
All metal substrates and fasteners – painted and unpainted – currently available, have been assembled on plywood panels using several different underlays and with some different eave flashings. The intention was to create all possible combinations of materials to assess the effect of such combinations, not just the materials alone but how they react with one another.
The panels comprised 12 different substrates -painted and unpainted, some new materials then in development and unpainted galvanised steel as a control. Four materials are mounted on each ply sheet and there are horizontal sections with normal at the base; inverted to expose the underside; then normal but protected by clear sheet to create an unwashed area at the top.
Four fastener manufacturers supplied four types of painted and unpainted screws in coated steel, aluminium and stainless steel which were arrayed across the roof panels in a staggered manner so that all screws have been installed on substrates in different order. No load spreading washers have been included in the latest trials.
So, the test roof (see image) has three horizontal layers of 12 different claddings with 16 types of screws arrayed over them. The roofs are mounted on steel-framed sheds specifically designed for the purpose and some of the newer test sites have individually designed racks or stands, such as at Taharoa, where three free-standing racks with current screws and some other materials are being investigated. At Limestone Downs there are also stands/racks specific to what is being exposed for the trials.
Much could be written about site corrosivity assessment but this is another article in itself as it is a very complex subject – suffice to say MRM has used both ISO 9223 and AS 3566.2 testing methods to see how the two (corrosivity assessment and assessment during exposure) are aligned. We now use just MS coupons, having determined this aligns with environmental assessment and is the most consistent method.
Site corrosivity can be measured by two methods – corrosivity of the atmosphere and the actual corrosion level of metal coupons. Both provide a ranking for the site where C1 is indoors and CX is extra severe.
Atmospheric assessment by Time of Wetness and Salt Levels
Time of Wetness (TOW) is assessed by the amount of time where humidity is over 80% and temperature is lower than 10 degrees. It is measured with a data logger at intervals of five hours to move around the clock. The project also uses NIWA weather station data.
Salt levels are measured with a salt candle which absorbs salt from the air onto a wet wick and the liquid is titrated for chloride. Titration is quite simple but the candles need changing and analysing monthly which is quite labour intensive along with doing the titration itself. The humidity and temperature are measured continuously by a data logger mounted near the candle and this measures how much time the site would be damp on a daily basis. The data from TOW and chloride levels are used in a formula to determine the C rating of the site.
Coupon exposure method
ISO also provides for assessing corrosivity by exposing metal coupons for various periods of time. The amount of metal lost by conversion into corrosion products (e.g. rust) over a period of time determines the corrosiveness of the site.
MRM sites
Both methods of testing – atmospheric or coupon corrosion – form part of how MRM assesses its sites. Whereas initially zinc coupons were used, wide variations in the composition were discovered and currently the trial uses 3mm or thicker mild steel coupons which are changed annually. They corrode rapidly and are less subject to alloy variation and are generally showing the sites as slightly more severe. The West Coast sites are more corrosive and Limestone Downs is by far the most corrosive of any of the previous test sites. The mild steel coupons are replaced periodically with the corrosive products on the coupons being removed to gauge the amount of corrosion that has occurred during exposure.
Finally, it has been shown that the corrosion ratings for all methods is quite wide and this means that two different locations can both be for Category 4, where the loss in one may be 400 gm/m2 loss and the other 650 gm/m2 loss – a difference of 160%. Category 5 can be from 651 to 2500 – a 230% difference. MRM has created decimal steps so that for example Category 4 sites might be 4.1 and 4.9 and be quite different. This method of assessment has been retrospectively applied when processing the latest data.
Outcomes after 5 – 6 years of the MRM Corrosion Project
Location | Coupon | C Rating |
---|---|---|
New Plymouth | PZ + 83 | 4.2 |
Invercargill | 83 | 3.4 |
Nelson | 83 | 3.1 |
Waipu | 83 | 3.2 |
Taharoa | MS (1) | 5.9 |
Muriwai - roof | PZ + 83 | 4.3 |
Muriwai - multi | All Zn | 3.7 |
Muriwai - multi | MS (1) | 5 |
Limestone Downs | MS (1) | CX 2 |
North Head | MS | 5 |
Farm | 3 |
When it came time to inspect the Nelson roof recently, every screw and substrate set became the subject of a very complex report which was subsequently broken down for each supplier and reported to them. It transpired that even when the appearance from the outside was OK the underside always showed some degree of haloing. Painted screws and washers were universally worse in this respect than unpainted of the same type. We have just repeated this exercise for the more severe Muriwai site with similar outcomes – still to be reported.
What this means
Such is the geography of New Zealand that many Kiwis choose to live close to the sea – areas classified as “marine” but this desirable setting falls into the category of a severe environment. The on-going research by MRM is revealing valuable information on what materials work best in these sought-after environments.
Although some of the fasteners supplied in the early days of the trials performed poorly, many improvements have been made and from this year onwards these assessments are expected to show vastly improved performance.