Oamaru Log House
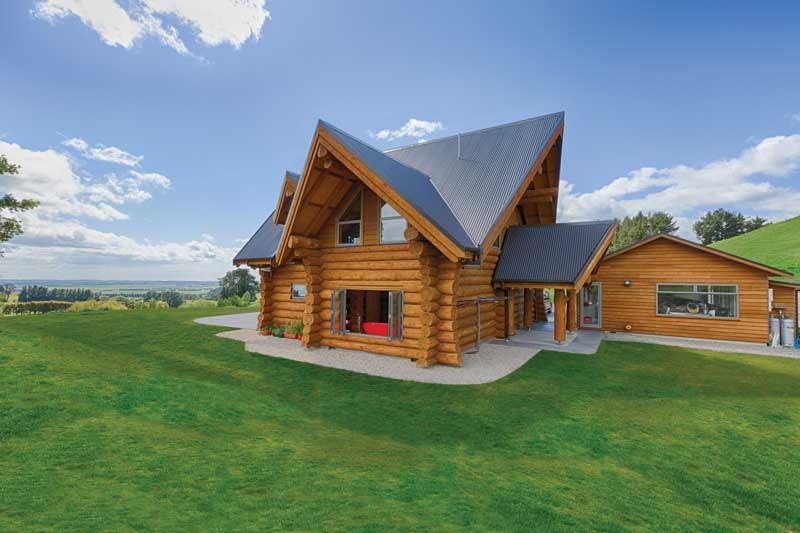
Building a sustainable, off-the grid house is a complex enough business but when you decide it’s also going to be a log home the difficulty goes up another level.
But Jeanne Gray had an experienced and dedicated team behind her when construction began on her dream home at Papakaio, north of Oamaru.
She enlisted the services of Natural Log Homes, run by Graeme Mould, who has been building log homes for 30 years. While Natural Log Homes was responsible for the log structure, High Country Carpentry laid the foundations, did the project management and oversaw the fit out and finishing.
Natural Log Homes enlisted the help of Geraldine architect Jess Paterson, who has collaborated with them for many years, to design the home.
“When I moved to Geraldine they were just up the road and they asked me if I would be interested in designing log homes,” says Jess.
“With log homes there is not quite the flexibility of design – you can’t have windows too close to log corners as you need to allow for the corner notching and the more corners you do, the more expensive it is, as this is the labour intensive part of the log work.
“You can’t have a 20m long log wall because the trees don’t grow that long and you also have to be able to transport the logs to site.”
Jess says she met Jeanne and discussed her options with Graeme at his log yard.
“She wanted quirky with cutesy little rooms and a sharp roof pitch. It was a very detailed log home with lots of junctions, dormers, soffits and things like the big central post that comes down the stairs that took lots of detailing.”
Jess says any design also had to allow for the building to settle under its own weight as the wood dries out.
“That’s one of the main differences of designing a log home is the settling that you have to allow for. The building drops in height about 4 per cent so that affects your chimneys, staircases, windows, doorways and you have to use things like two-part flashings.”
Jess says they use devices such as “buck boards” that allow for settling. “They go along the top and slide down over the window and you adjust them over time – you plane it off then re-fit it and after about five years the house has settled and that’s it.”
She says “hurricane rods” are run vertically through holes drilled in the logs and these threaded metal rods, which help to hold the stacked logs together, can be are tightened over time as the house settles.
“You also have to make sure that any future openings avoid the hurricane rods, and you have to plan out where all your electrical outlets and plumbing is going to go beforehand so holes can be drilled for those.”
Lain Hellmrich, owner of High Country Carpentry, says he enjoys the handcrafted nature of log homes.
Because Jeanne’s home was in such a remote location, his team of 8-10 builders were on site for about 10 months and during the week they all stayed at Papakaio House, which used to be the local store.
“When we got there Jeanne had beds made up for us all and she’d have dinner cooked for us all when we got back at the end of the day,” Lain says. “And when we were working she would bring smoko down to the site.”
The home’s log superstructure was cut and assembled at Natural Log Homes’ yard before being disassembled and trucked to the building site. Untreated Douglas fir logs were used with all the corner notches and long grooves scribed and cut by hand to ensure a tight fit.
Each log is scribed and cut so that they look like they grew together. Scribing transfers the contours of one log onto the contours of the log above. When the timber between the scribe lines is carefully removed, then the logs fit each other perfectly. A double groove is cut the length of the log and a gasket is fitted in each groove to prevent water ingress.
Corner notches where the logs cross over are done in a “saddle notch” style that ensures a tight fit for the life of the building.
Lain says his crew laid the concrete slab for the
house and the separate garage at the same time.
One of the reasons that Jeanne decided to go off-grid was that it would have cost a lot to bring power to the site. However, that meant the builders had to use generators for their power.
Lain says they built the garage first and got the solar array and batteries set up so they had power and weren’t so reliant on running generators all the time.
He says the log structure was assembled on site
in a matter of days, and then began the mammoth task of finishing the home.
“The scale of the job was immense,” says Lain. “You look up 8m to 9m to the ridgeline of the house. We had to build a whole scaffold inside just to do the tongue and groove lining on the ceiling.”
The roof has a double layer of insulation with the rafters being lined with tongue and groove macrocarpa. Above that are a 12mm diaphragm and the secondary roof structure over that with thick insulation between the two.
The log walls have high R values themselves, and the home has underfloor heating of the concrete slab via solar hot water or from the wetback on the owner’s woodburning Rayburn range, which she also cooks on.
The home is able to function for five days without solar gain and has a gas oven and back-up generator if needed.
Lain says one of the most time-consuming aspects was installing and detailing the home’s distinctive gabled roof, executed by Canterbury Long Run Roofing.
“The roof was a real work of art,” he says. “The roofer was there day-in, day-out; he did all the cuts on the flashings, valley cuts and raking cuts on the gables that are all exposed. There are so many gables – it’s like a ship’s prow with double or triple fascias.
Lain says the timber was specially milled for rafters and fascias so they could have single lengths – some up to 8 metres long. He finds it fascinating the way log homes move as they mature.
“It’s like a living thing the way it settles, and it’s a massive settling process so you have to have a method built into the structure to allow for that – it’s almost like creating a mechanical device.”
He says the detailing of the internal fit-out was time-consuming and complex.
That detailing was recognised when the house was named 2016 Registered Master Builders House of the Year (Mid and South Canterbury region). The home also earned the overall Craftsmanship Award, along with Gold, Sustainable Home and Category Winner awards for the region. It then went on to win National Gold Reserve, making it one of the top 100 home builds in the country. The national judging panel commented that “this is a complex project that required a challenging construction method using unconventional building materials … given the nature of this type of construction, the builder’s craft was amazing in every respect and a worthy winner”.
While log homes can have a rustic look, Jeanne has spiced hers up with colour accents and an exposed aggregate floor. Bold reds feature in the kitchen cabinetry and in the bathroom, with a fire engine-red bath. Oranges and greens also break up the largely neutral colour palette and wood tones.
The home has three bedrooms, a library, two bathrooms, a double-height living space, and a kids’ loft.
Lain says creating such a unique home was a team effort, and Jeanne’s ambition was rewarded.
“It’s such a neat place and I’m super proud of the way it came up,” he says. “Jeanne wanted a base for her grandchildren and they love it up there with the house sitting on the hill and having great views.”