Domaine Thomson Wines
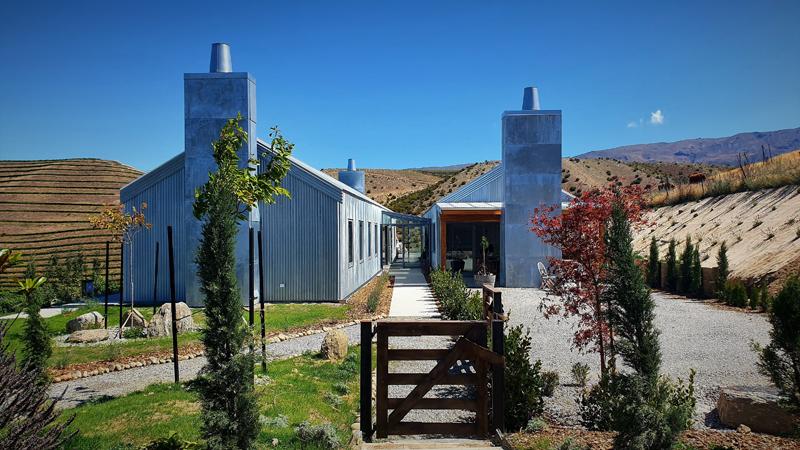
Just as Domaine Thomson Wines showcases the best of the Central Otago and Burgundy terroir, the company’s new cellar and tasting room takes design cues from these two distinct regions.
On the outside, the architecture is reminiscent of the back country huts of Central Otago, and references honest structures that were modestly clad in various materials including weathered galvanised corrugated iron. On the inside, there are elegant French references such as the herringbone wooden floor, wooden cobbled floor, whitewashed walls and metal chandeliers.
The building ties together the company’s Cromwell origins and its French connections, with Domaine Thomson making wine from its pinot noir vineyards in Central Otago and from parcels of pinot noir and chardonnay vines it owns in Burgundy.
It planted its 14ha vineyard in Central Otago in 2000, and more recently acquired the parcels of French vines.
The new building – housing a cellar door, tasting room, library, cellar, staff facilities and an office – now allows Domaine Thomson to tell its story and promote its products to wine enthusiasts, something it has been keen to do for a long time. It also provides visitors with stunning views over Cromwell Basin and Lake Dunstan.
Domaine Thomson Wines Manager Kate Barnett said, “We are an established brand so we have been looking forward to building a ‘home’ to showcase our wines from France and Central Otago.
“With our background as an organic certified and bio dynamic vineyard, we wanted the building to have a more natural feel.”
To that end, architect Noel Lane explored the back-blocks of the Central Otago countryside with vineyard owner David Hall-Jones, researching back country hut typology.
The family-owned vineyard has a close affinity with the history of the area and John Turnbull Thomson, chief surveyor of Otago in the mid-1800 and David Hall-Jones’ great-great-grandfather. He named well-known landmarks such as Mt Aspiring, Mt Earnslaw, Lindis Pass and the Pisa Range – the latter overlooks the new building.
Noel Lane’s concept design was a building with corrugated iron roofs and walls, a lean-to porch and galvanised sheet chimneys. The design has two ‘huts’ connected by a glazed entry and corridor – one hut contains the cellar door, tasting room, gallery and library; the other has the cellar, office and staff amenities. The two huts are set at a slight angle to each other to welcome visitors into the heart of the building.
Architects Noel Lane and Tom Rowe (of R B Studio) have successfully collaborated together for many years and completed a number of award-winning projects. After the initial concept was approved, both architects worked together to refine and deliver the project. To execute the design effectively, they continued to research images and archives of back country huts. As a result, the detailing evolved with a careful balance between concealing material junctions and expressing the structural junctions in a way that reflected the deliberate manner these buildings were put together.
The process involved developing an understanding of how historically back country huts were put together and then, correspondingly, how this could be replicated to comply with current regulations. Examples are illustrated in the chimney design and materiality, or corner junctions and in the notable absence of a spouting. All consistent with the typology used in back country huts.
Kate Barnett said using corrugate cladding and roofing meant an efficient and cost-effective build and they got the character look they were after by using Roofing Industries’ True Oak® Corrugate, a return to the original deeper, rounder corrugate roofing and cladding shape that dates back to the early 1800s. However, they didn’t want coloured steel so they decided to use vegetable acid to age the True Oak® Corrugate’s 0.55 galvanised steel.
Breen Construction and RB Studio conducted trials on sheets of True Oak® Corrugate to get the aged look the client wanted.
Kate said, “We were really happy with the look and the fact that it was an organic product that was used to achieve it because that ties in with our organic, bio dynamic approach to wine making.” Architect Tom Rowe said there were two factors at play when it came to the weathering of the corrugate: one of them was to make it look like an established back country hut in the South Island but the other was a resource consent requirement to reduce the reflectivity of the cladding. While the acid-induced weathering of the True Oak® Corrugate compromises the material’s integrity, the client was comfortable with this on the basis that local buildings have endured over time. The application of the vegetable acid was controlled and superficial and was washed off within 24 hours. On the walls, the corrugate is effectively a rain screen with a cavity system and waterproof barrier behind it.
Roofing Industries Cromwell Manager Dave Hansen said that weathering the product for use in a coastal environment would not be recommended but was less of an issue in a non-corrosive environment like Central Otago.
“It’s a different look that showcases the True Oak® Corrugate product,” he said. “It’s not the first time I have seen it; there was a job in Queeenstown where they used spirits of salts on the product and played around with it to get the level of patina that they wanted.” Dave said while the design of the building was going for a “basic, rustic look”, some of the detailing on the roofing and cladding was tricky to execute for Roofing Industries and the installer, Attention To Detail Roofing.
Dave said, “We spent hours and hours getting the 0.55 galvanised steel chimney panels all prefolded and ready for the installer. Each section on the chimney consists of three panels – a left, a right and a centre panel – and they all had to be folded precisely.”
Courtney McDowell, of Attention To Detail Roofing, said the whole team brought their expertise to bear when rising to the challenge of executing a tricky and technical job.
He said elements such as the chimney detailing, the roof folding over to form barge boards on the walls, crush fold detailing around windows, and the cladding folding around the corners of the building made for a challenging but enjoyable job. “Because the owners wanted to get the look right, we had a bit of time to do trials of the chimney panels to get them to click together. There were six sections consisting of a number of panels on each of the three chimneys, and because they wanted a flat panel look – not a ribbed profile – we had to design a hook join to lock the panels together and make the joins waterproof.
“We also had to take into account internal gutters behind two chimneys and an external gutter on another chimney to stop water running down its front.”
He said the crush fold detail around the windows was tricky to execute and flash compared to a traditional flat surface, and detailing around the windows meant cutting with the grain rather than across the grain of the corrugate, which was also challenging.
And there were no corner flashings as the cladding folded around the corners of the buildings.
“That was the real tricky part, folding the wall around with a window either side of the corner because there was no square point to measure from, and the 0.55 gauge is much harder to fold than the 0.40.” The effect of all this detailing is to make the buildings look softer and more organic.
As well as the corrugate cladding and roofing, there are other traditional elements to the building such as the timber post and beam construction, and exposed trusses. The glazed entry with stone floor connects the two ‘huts’ and serves a traditional porch/breezeway function before guests enter the interior proper. The cellar door area has a wooden cobbled floor, made up of 3600 free-standing hardwood end grain cobbles for texture. The variation of material demarcates a threshold space, traditionally associated with back country huts for sheltering horses from harsh winter storms. As a material, end grain cobbles are something that might be seen in French historical buildings. This threshold space is located between the tasting room on one side and the gallery/library on the other, each with a large fireplace.
Indoor finishes include exposed Douglas fir, macrocarpa and slabs of Mt Somers limestone around the fireplace.
Along with the cobbled floor, there are other old-world French references such as metal chandeliers and the herringbone floors in the tasting room and library.
The overall feeling of the building is rustic yet refined, and reflects the history and unique character and connections of Domaine Thomson Wines. As Kate Barnett said, “We are so happy with our new home, it looks like it has been here 100 years and sits so comfortably in the landscape.”